News

December 3, 2019
Digital Logistics set for full commercial launch
Q1 2020 marks the full commercial launch of Digital Logistics.
– Today base-, rig- and operator-companies lack a general overview of their supply chain and movement of goods and Cargo Carrying Units (CCU`S). Our Digital Logistics System puts an end to this, and provides offshore- and base-companies with a whole new tool to plan and execute their daily logistical operations, Camilla Nylund, Managing Director in Optilift says.
Previously granted R&D-support from the EU-commission, the Digital Logistics system has been developed as an additional component to the traditional Optilift product Motion Reporter.
Where the Motion Reporter measures relative heave-movement between the supply vessel and the boom tip of the crane, the Digital Logistics system keeps an overview of all cargo transits between onshore base, platforms, rigs and supply vessels, all stemming from the camera-sensor mounted at the boom tip.
Real-time operations
Digital Logistics will allow users to plan and book CCU shipments in advance, in effect creating “Just-in-time” deliveries.
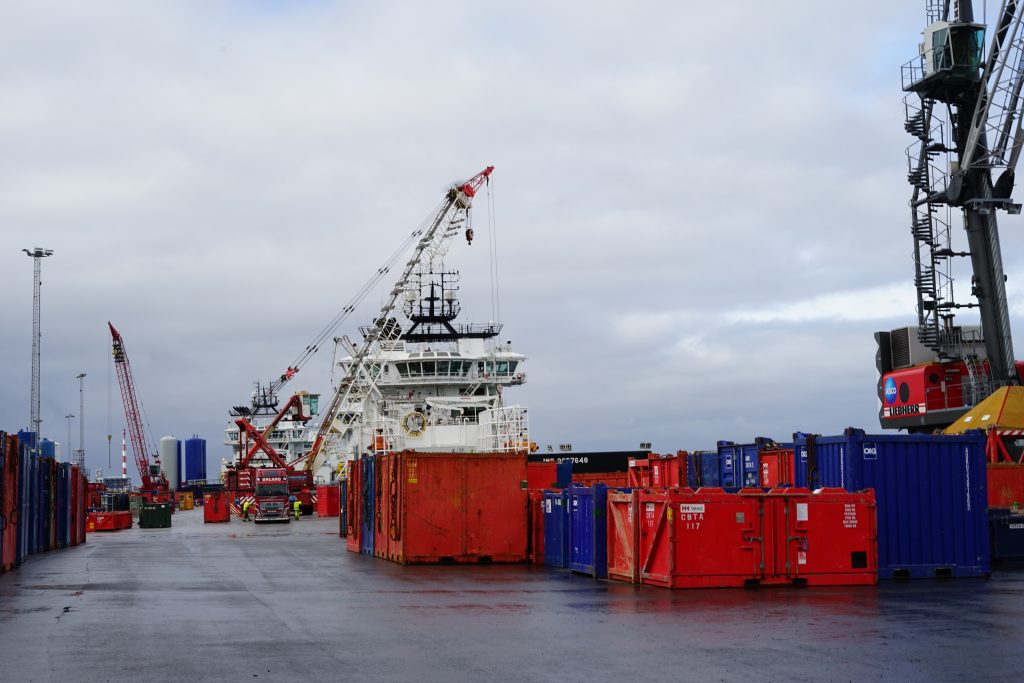
– Today a common logistical operation is to send important equipment offshore weeks or even months in advance of its use, to make sure it has arrived at the platform by the time it is needed. This is not very effective, and is a form of cloaking of the logistical eco-system, says Nylund.
– Advance booking will ultimately reduce the need for supply-boat storage, and further reduce the amount of sailings needed. In short, your logistical chain will gain a new and trusted flow – which can be monitored 24/7. CO2-emissions are also reduced as an effect of more optimised sailing and vessel utilisation, she explains.
Eliminate time-waste
Another growing concern today is an increased amount of offshore time-waste connected to manually logging CCU location and searching CCU`s for the right equipment needed.
– We receive a lot of feedback from offshore workers who are tired of the unnecessary time they waste because no-one really know where different equipment is located.
– Through Digital Logistics platform managers or others will get an instant preview of all CCU`s, their positioning and contents. This would drastically reduce, if not eliminate, such time-waste.
– Realtime CCU locations enables onshore and offshore personnel to share a common understanding of the available deck space, avoiding equipment being sent out when deck space is scarce, thus reducing the amount of equipment on roundtrips. Improved planning would also reduce the amount of internal lifts, in this way reducing risk.
A small but important feature of the system is also alerts.
– For example, if a CCU exceeds a legal weight-limit, the system will alert the user so he can solve the problem. The system could also oversee that procedures linked to dangerous goods are followed, and inform of containers being idle for too long.
– This results in safer logistical operations, and calls for a new and improved way of interacting with users, Nylund states.
Cloud only
Except from the Optilift camera-sensor mounted at the crane boom tip, no installments of any physical gear on any containers or other physical environment is needed for potential clients to carry out using the Digital Logistics system.
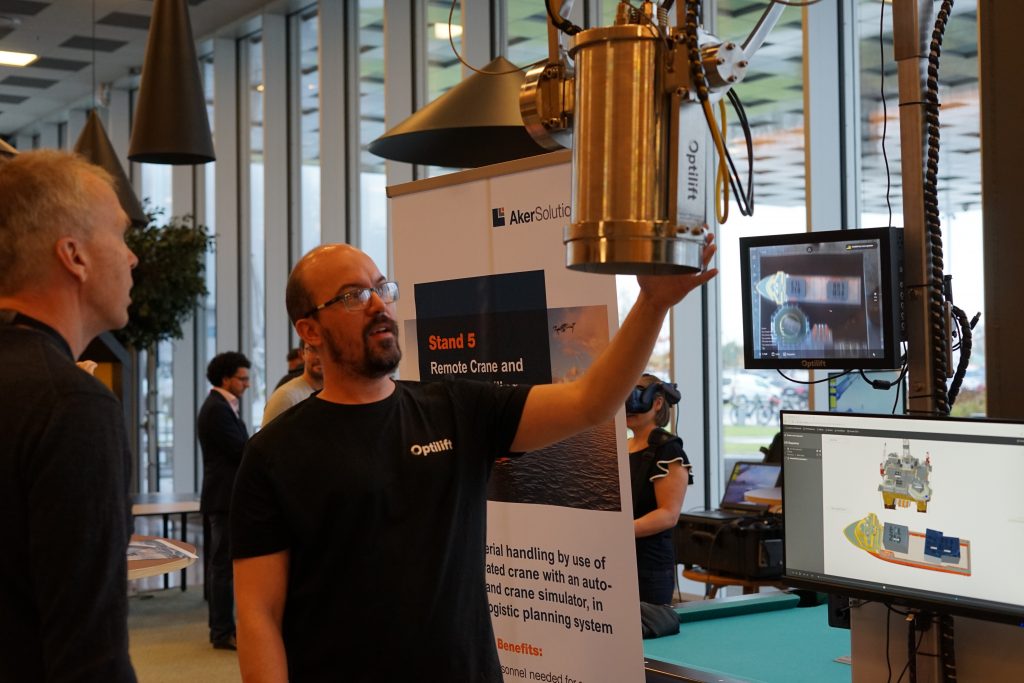
– Integration between ERP-systems is also possible, wether it be SAP or any other, she adds.
Companies such as Aker BP and recently ASCO have been involved in the pre-commercial development phase of the system.
– Their input and feedback has been extremely valuable for Optilift, and we look forward to any future co-operation with them.