Offshore
Working in harsh
environments
Optilift offers products that improve safety, efficiency and logistics flow in cargo handling offshore.
Our solutions can be retrofitted to existing cranes and machines, and pave the way for remote controlled and autonomous operations.
Benefits
- Handle cargo transfers faster and more cost-effective
- Reduce risk of human injuries on deck and help prevent damage to cargo
Learn about ways to reduce risks related to lifting operations and reduce CO2 emissions related to sea transport.
Products
Lifting Support
A group of products that are designed to help on-site crane operators to perform safer and more efficient lifting operations.
Motion Reporter
- Measures the relative heave-movement.
- Enables less waiting for weather.
- Helps avoid lifting in unsafe conditions.
- Does not require instrumentation of the supply vessels.
People Detector
- Detects people and highlights them on screen for crane operator.
- Enables early warning on dangerous situations.
- Enabler for remote- and autonomous crane operations.
Boom Tip Indicator
- Shows where cargo will land
- Helps crane operator avoid lifting with off-/sidelead angle.
Soft Lifting Assistant
- Helps perform soft landing and lift-off.
- Uses the actual heave movement to help timing of the lift.
Digital Logistics
Digital Logistics keeps an overview of all cargo transits between onshore base, platforms, rigs and supply vessels. The Deck Planner allows easy overview of cargo and deck, and planning of lift sequences with intuitive drag and drop interface in the web browser. The Lift Reporter runs on Tablets and the Crane monitor, integrates with the Deck Planner, and shows the lifting sequences live on the screen.
Maps
- Shows real-time images of the vessel deck, platform deck and quayside areas
- Easy access via Deck Planner web application.
Deck Planner with Cargo Tracker
- Shows location of cargo in real-time.
- Plans and communicates lifting sequences to the crane.
- Sends events to subscribers on cargo- and vessel movements.
Site Observer with Cargo Tracker
- Identifies and tracks cargo locations.
- Builds and maintains 3D models of quay sides, site decks and vessel decks
- Shares cargo events with customer logistics system.
Smart Gate – CCU Portal
- Detects and identifies cargo arriving and leaving at gates.
- Notifies connected systems of the cargo event.
- Takes pictures of the cargo.
- Updates the digital twin.
- Creates a visual ID for further tracking.
Lift Reporter
- Shows the lifting tasks planned with the Deck Planner.
- Highlights which CCU to lift, and exactly where to place it.
- Shows special procedures for dangerous goods.
Assistance Systems
A group of products to assist and automatically control parts of crane operations, for retrofit on existing cranes, or integration to newbuilds. The features can be used for local control of lifting operations from the crane cabin, or in combination with remote control and autonomous lifting operations.
Assistance Systems
- Provides features to assist and partially automate lifting operations.
- Useful for local control of lifting operations from the crane cabin.
- Enabler for remote control and autonomy.
Auto Landing
- Times the landing based on real-time velocities and prediction.
- Press and hold a button on the joystick to activate and execute.
- Ensures soft landings without re-entry.
Auto Lift-Off
- Times the lift-off based on real-time velocities and prediction.
- Press and hold a button on the joystick to activate and execute.
- Ensures soft lift-offs without re-entry.
Relative Heave Compensation
- Automatically compensates for relative heave motion between crane and vessel.
- Enables constant tension on wire-rope for empty hook and light-weight loads.
Anti-Pendulum
- Ensures pendulum movement does not occur during lifting operations.
- Actively compensates for pendulum movement if inflicted by external forces.
Anti-Collision for Cargo
- Ensures that the hook and cargo does not hit structures on the vessel and platform.
- Adapts automatically to structural changes on the platform.
Anti-Collision for People
- Prevents hook or cargo from hitting people.
- Ensures lifting does not occur over areas with people present.
- Actively stops the crane before the cargo reaches people.
Anti-Collision for Boom
- Detects static and moving objects in the lifting area
- Stops the crane before the boom hits obstacles
- Only the crane is instrumented
AutoHook Control
- Automatic on- and off-hooking without deck crew on vessels and platforms.
- Requires cargo carriers to be equipped with the AkerBP AutoHook.
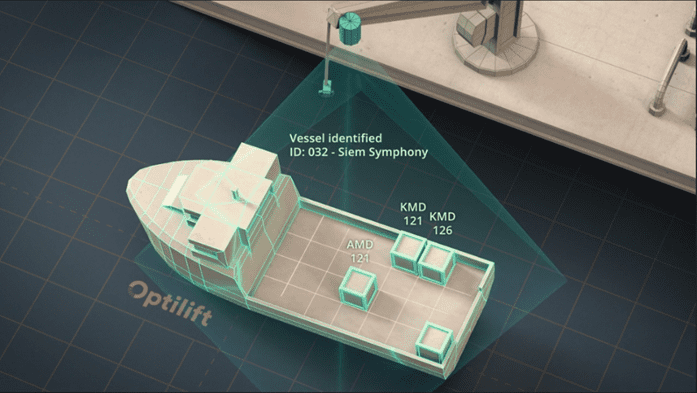
Cruise Control
- Follows the supply vessel’s horisontal movements during sea lifts.
- Enables hands-free crane operations while waiting for the right moment to perform the lift.
- Requires the Anti-Pendulum feature.
Assisted Autonomy
Optilift offers features for remotely monitored autonomous control of crane operations, where the control of the crane is located far away from the crane, onshore or on another rig. The solution can be retro-fitted to existing cranes or integrated into newbuilds.
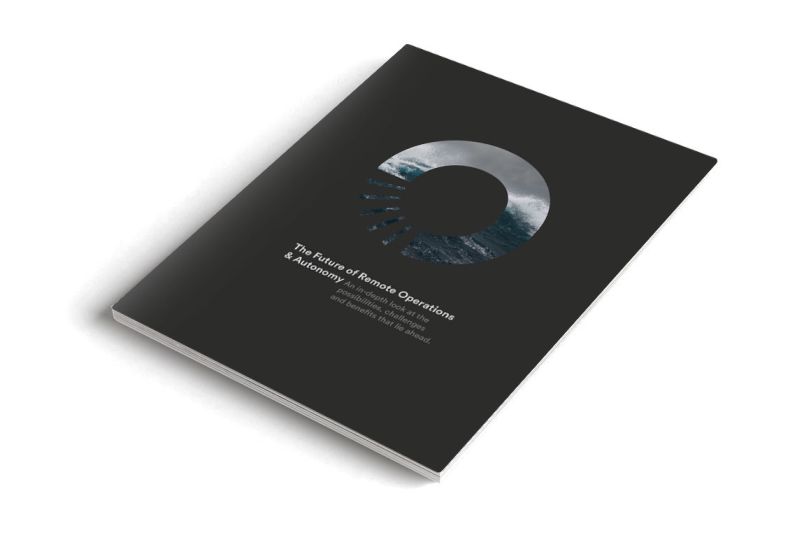
Introduction to Remote Control and Autonomy
The Remote Control & Autonomy product group offers features for autonomous and remote control of crane operations, where the control of the crane is located far away from the crane, e.g. onshore or on another rig.
Autonomous Crane Control System
Optilift has together with Aker BP developed the Autonomous Crane Control System for use with offshore cranes.
The system has been demonstrated during a full-scale test in Egersund, July 2021 and furthermore tested and reached TRL4 offshore at Valhall IP during 2022.
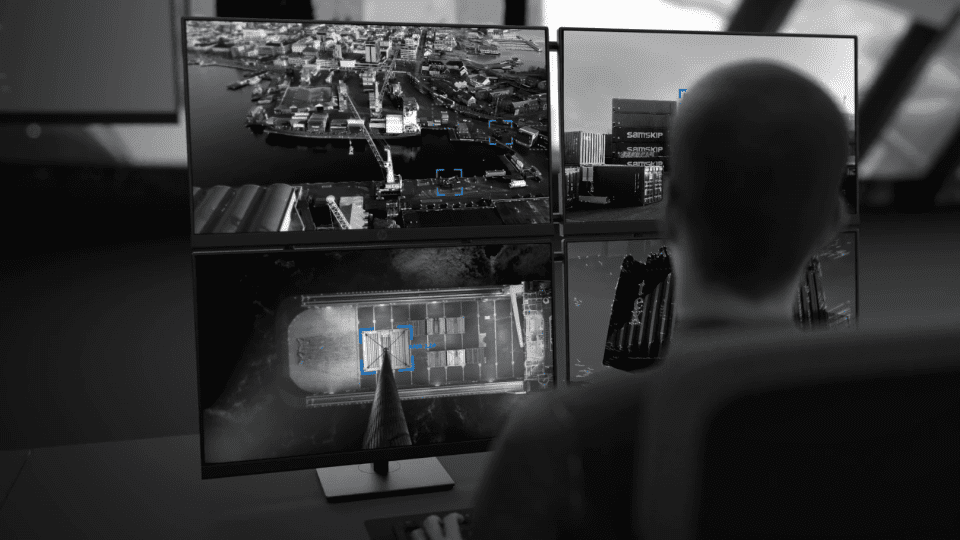
Remote Control Room
- Enables remote operations.
- Real-time and low-latency video and audio from remote machine.
- Provides “Assisted Autonomy” by planning lifting sequences using Deck Planner or cargo movements using Yard Planner.
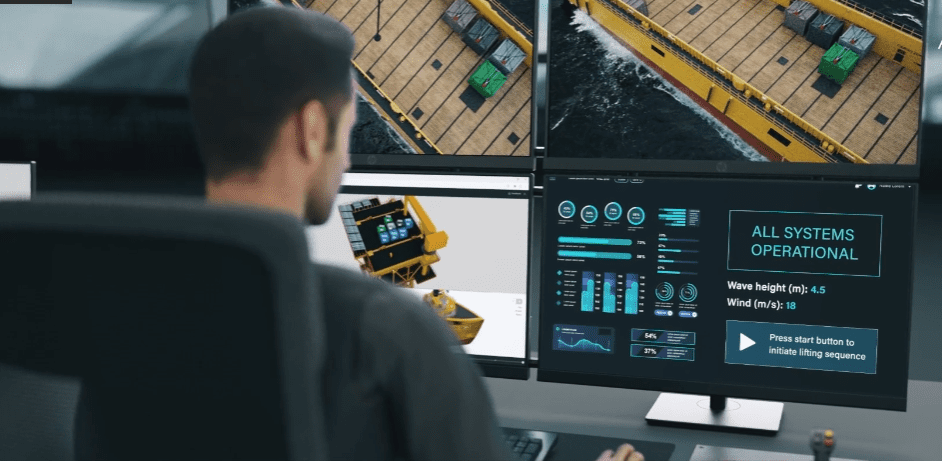
Live Support Centre
- Automated reporting of technical issues.
- Proactive trouble-shooting and repairs.
- End user support and training.
The process
Our technology is adaptable and versatile, and can be implemented by our customers in a step by step- process.
Step 1 Digitalize
Moving from manual processes to digitalized and automated handling, with integrated systems and simplified procedures.
Step 2 Perceive
Installing cameras and configuring software for automatic capturing of physical events and cargo movements, and reporting them to the digital twin.
Step 3 Optimize
Alerting for bottlenecks and improving daily work processes and reaping the benefits of automated perception and digitalization technology.
Step 4 Remote-Control
Moving operators away from the dangerous areas to a central control room and improve flexibility of staff and travelling.
Step 5 Autonomy
Optimizing the operations by converting the operators to supervisors, while machines perform cargo handling autonomously. Multiple machines monitored by a single human supervisor, fully utilizing the power of autonomous cargo handling.
Testimonials
– The cost of the Optilift system fitted on our main crane paid itself off in one lift. A major delay due to weather conditions would have come at a substantial cost. – The Optilift system helped us proceed with the well operation and to get it ready for production as planned. That saved us a lot of money. If it were up to me, I would have the Optilift system mounted on all our offshore cranes, says the Well Intervention Supervisor.
The Optilift Motion Reporter technology has at least once saved our client Ithaca Energy up to a full dayrate in costs, as the technology has made it possible for us to continue to load supply-goods from supply vessels – when we probably would have shut down rig operations, without the information from the Optilift Motion Reporter.
Optilift has proven throughout 2017 to be a very useful tool. On several occasions, the significant wave height reported from the control room was significantly higher than what Optilift reported as the actual movement on the specific part of the vessel deck. This has made it possible to perform a lot of lifts that would not have been possible without Optilift.
We had a lift of 57 tonnes where we saved 20 days because the lift could be performed with up to 2,5 meter waveheight, compared to traditional 1 meter. Statistics show that it is approximately 10 times more days when these operations can be performed when the limit on wave heights is extended from one to 2,5 meters. In this single example we reduced costs in the order of 600 000 NOK per day, or somewhat above 10 MNOK for the entire operation, says the client.
I am operating several cranes on our platform – one of them is without Motion Reporter, and I feel “blinded” without the Boom Tip Indicator – it improves my day-to-day effectiveness during lifting.
We managed to get the BOP on-board as scheduled – this would not have been possible if it was not for the Motion Reporter.
This winter, with Optilift, was actually the first winter we did not have problems with getting our cargo on board.