News
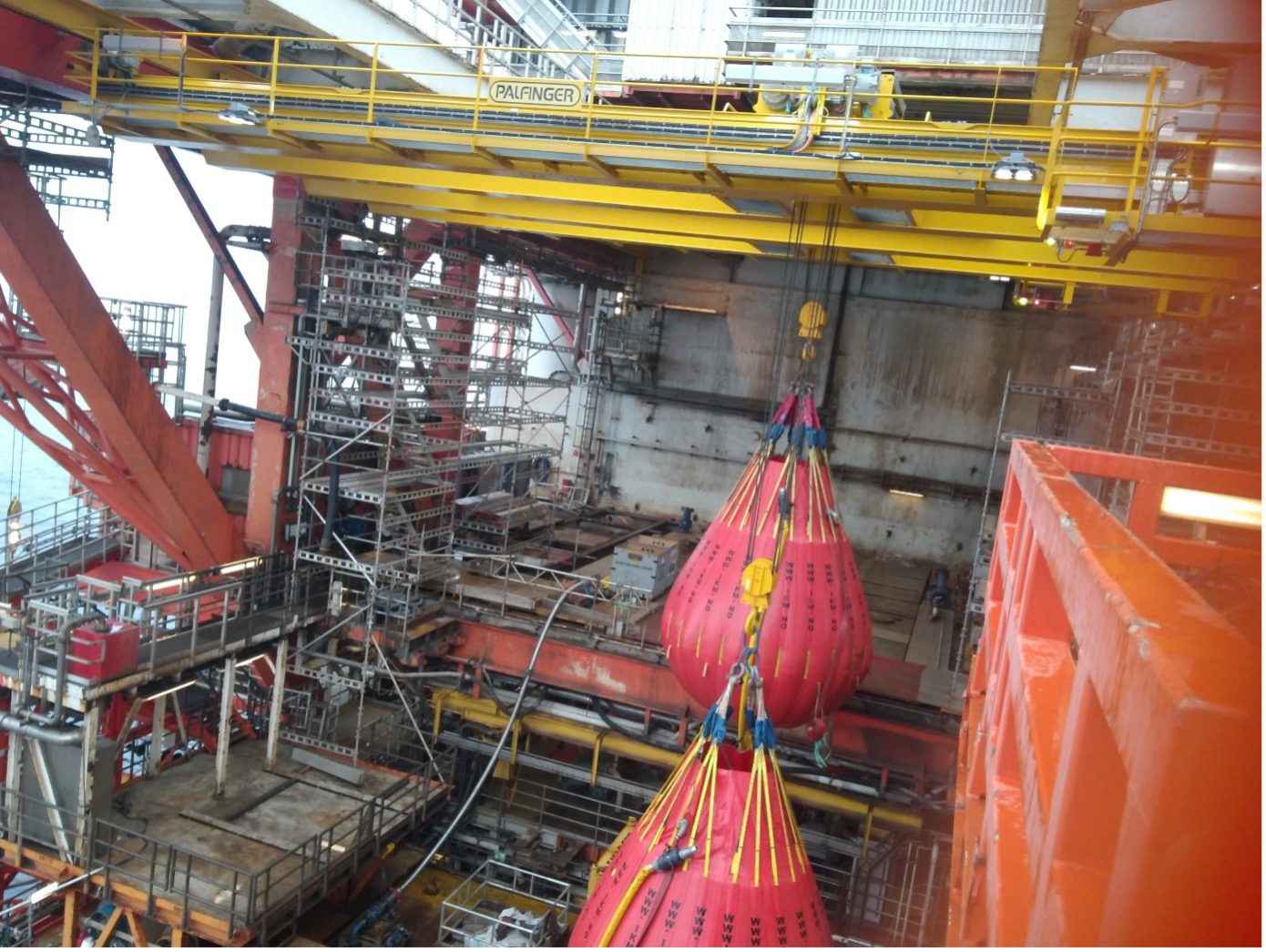
June 11, 2021
Laser sensors from Optilift deliver safety for overhead cranes on Valhall Oilfield
Since August 2020, two electric overhead travelling cranes fitted with Optilift´s advanced Ex-certified anti-collision laser sensors, have been operating on Aker BP´s Valhall Oilfield in the North Sea.
The cranes, which are delivered by Palfinger, handle Wireline and well intervention equipment and containers on the platform deck. Optilift´s lasers detect obstacles like drilling riser and is part of the cranes anti-collision system. When multiple tasks are performed on the platform, there is an increased risk that objects end up in the path of the moving crane. A collision has a big potential for harming personnel and damaging equipment. Optilift´s laser-based anti- collision system effectively detects when fixed or moving objects come too close, and automatically stops the crane traveling motion.
Ingvald Martin Framnes, senior engineer in Aker BP and responsible for crane & lift operations, is satisfied with the performance of the lasers from Optilift.
« We have applied the laser sensors on two new electrical overhead travers cranes on the Valhall IP platform in connection with ongoing rehabilitation projects. In particular, we had to build a scaffold in the working path of the cranes. By instructions from Optilift, a laser detection plate was installed on the scaffolding, utilizing the laser sensors to detect the plate and so helped us to avoid any collisions with the scaffold and other equipment during the operation. They proved to be a reliable and secure technical barrier in addition to operational measures », says Framnes.
Jan Silgjerd, Head of Application Engineering at Palfinger Marine Norway AS, about the Laser sensors from Optilift, delivered as part of the electrical overhead crane from Palfinger – “It has always been a challenge to find a good and reliable system for detection of collisions with risers and other objects in the riser area. In the past we have designed multiple mechanical arrangements, and experimented with different type of light and lasers, but all of them have had challenges with fog, dirt or mechanical reliability. The new sensor from Optilift looks very promising so far and seems to be by far the best solution we have seen to solve this problematic safety concern.”
Increasing safety
Torbjørn Engedal, CTO of Optilift, is pleased with the feedback from Aker BP and Palfinger. He believes that the laser sensors are more reliable than the traditional means of collision prevention.
«Manual tripwires have been commonplace in the industry. They are connected to a swich which turns off the crane when the tripwire hooks up to an emerging obstacle.
Our lasers are fitted on both sides of the electrical crane and measure distance along the span of the crane. When the beam is cut off by an object, the crane stops automatically», says Engedal.
The Optilift Laser Sensor measures distance to objects and outputs signals either via a digital interface or in the 4-20 mA range. It is designed to monitor the moving path of an overhead traverse crane. In addition to acting as a contactless trip wire, it can be used for other barrier- or distance measurement purposes.
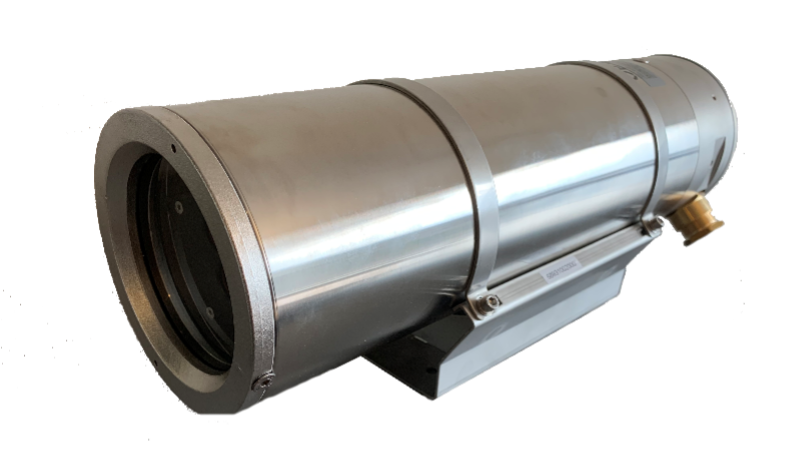
The Optilift Laser Sensor contains a processing unit that detects noise and can report loss of signal and noisy measurements in addition to the actual distance to the nearest object.
The unit is prepared for remote software upgrades, including remote diagnosis and troubleshooting when wired to an internet connection. Optilift can deliver customizations to processing and logging, local and remote, says Engedal.