News
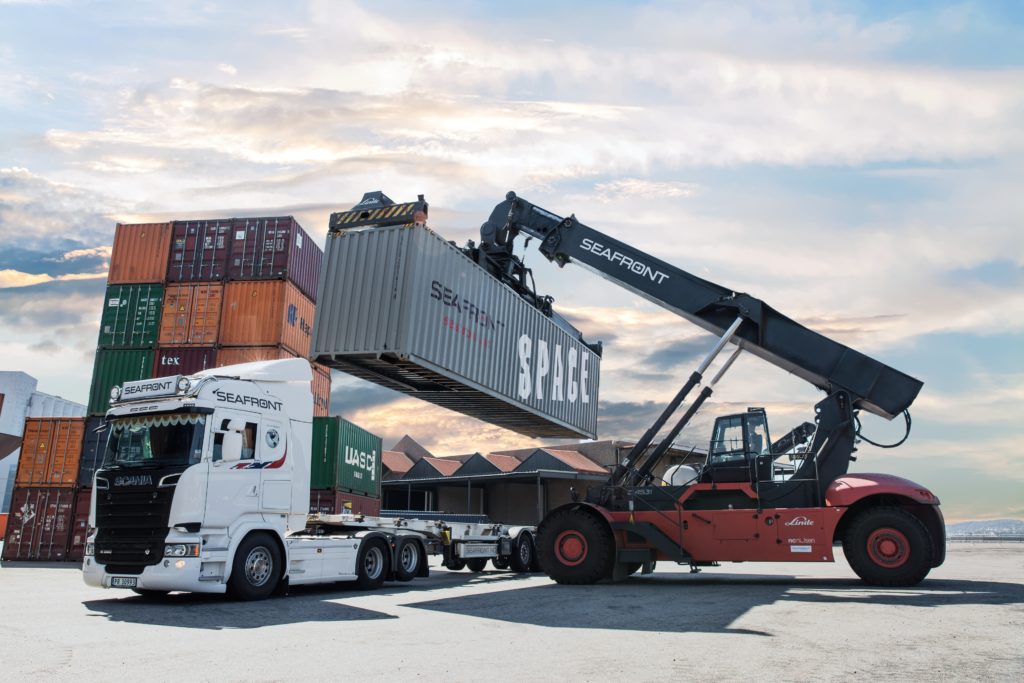
September 5, 2022
Safer and more efficient cargo ports
With advanced sensor technology, camera recognition and AI, Optilift will make ports and freight terminals work smarter.
The technology is now being deployed in Port of Kristiansand, in collaboration with the terminal operator Seafront Logistics. Cameras that capture all container movements are to be mounted on two reach stackers and in the terminal gate. A vital part of the project is cloning the harbour in real time. A logistical digital twin of the port area will be created and automatically updated, enabling operators to simulate loading, and unloading operations. The planning tool helps operators organizing their workday better.
Seafront Logistics is a leading port operator and freight forwarder, with port service terminals in Oslo, Larvik, Kristiansand, and Stavanger. With 25,000 square meters of storage area, Seafront handles more than 40,000 containers annually at its ports. Kjetil Hansen, general manager at Seafront Logistics, says he looks forward to testing Optilift´s innovative solutions.
“Digitalisation and sensor technology open up new opportunities for streamlining cargo handling in ports and terminals. To retain our position as a leading operator of ports and cargo, we at Seafront must adopt new technology. Competition in the industry is strong, and financial margins are pressed. We will have to cut costs and increase efficiency,” says Hansen. The deployment program is supported financially by the Norwegian Coastal Administration.
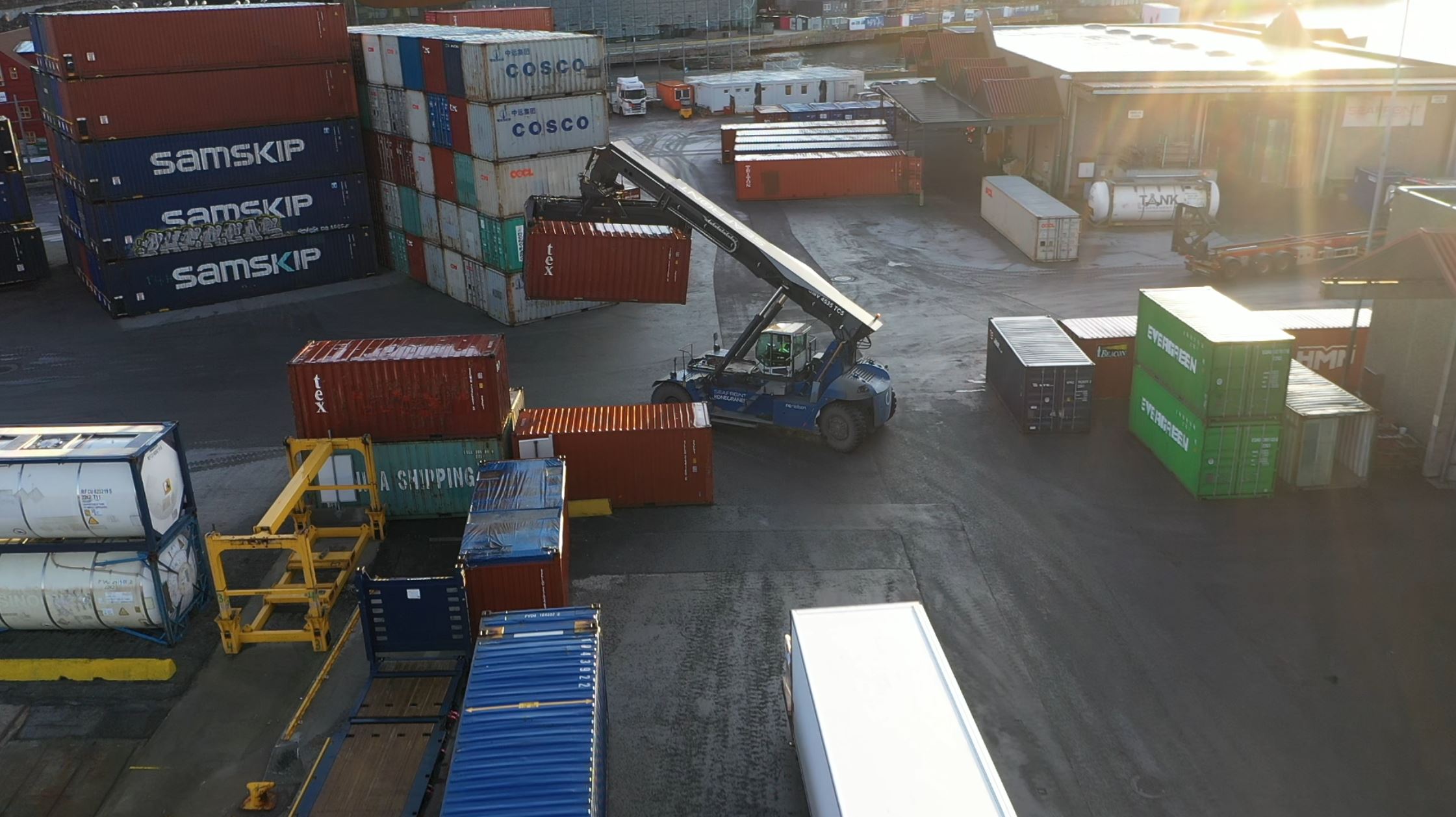
Great potential
Torbjørn Engedal, CTO at Optilift, says the technology has been developed at Optilift’s parent company, VOCA. Digitizing work processes in harbours and terminals carries great potential.
“It’s all about moving more goods faster, safer and with fewer resources,” says Engedal.
The key is to get control over the flow of goods between ship, port, warehouse, and truck. To automate the flow, accurate information is needed about where each individual container is located and where it is going. Optilift’s recipe is a camera-based system that reads the identification tags on all containers and tracks the movements in real time. The system can be mounted on all types of cranes, forklifts and other mechanical equipment that handle containers in ports and terminals. With precise knowledge of where the containers are at all times, loading and unloading operations can be optimised.
“This makes it possible to plan loading and unloading operations, so that containers are handled in the right order, and arrive where they are supposed to at the right time. With time saved, ships spend less time in the ports, and goods arrive faster at their destination,” says Engedal.
Fewer injuries
With a digital twin and planning tool in place, the road is paved to automation of loading and unloading operations. Cranes, reach stackers and forklifts can be controlled remotely from the control room, and eventually run completely autonomously. With fewer people in close contact with containers and goods, the risk of personal injury is reduced.
“Optilift´s solutions can be deployed step by step, with features like live cargo tracking, people detection and obstacle avoidance, and soon all the way to full scale autonomy”, says Engedal.
Cutting costs
Kjetil Hansen in Seafront believes that great things will happen in digitization and automation in his industry in the next few years.
“Loading and unloading operations and storage are repetitive tasks suitable to automation. We work at all hours of the day and night when ships dock, and many people are involved. Wage costs are substantial, and there is always a risk of accidents and human failure in places where people work close to large machines and heavy loads», says Hansen.
He does not fear that new technology will make people redundant in the ports. Rather the opposite. “We will not need fewer employees in the future. Instead, they will be given new tasks. We will need more employees with technical expertise in several fields. Digital planning, remote control of operations and machines and cranes that are fully or partially self-driving, will free up capacity. We can thus move more goods with fewer hands. Our employees will no longer move pallets manually but perform more specialized tasks. The future is promising, says Hansen.