News
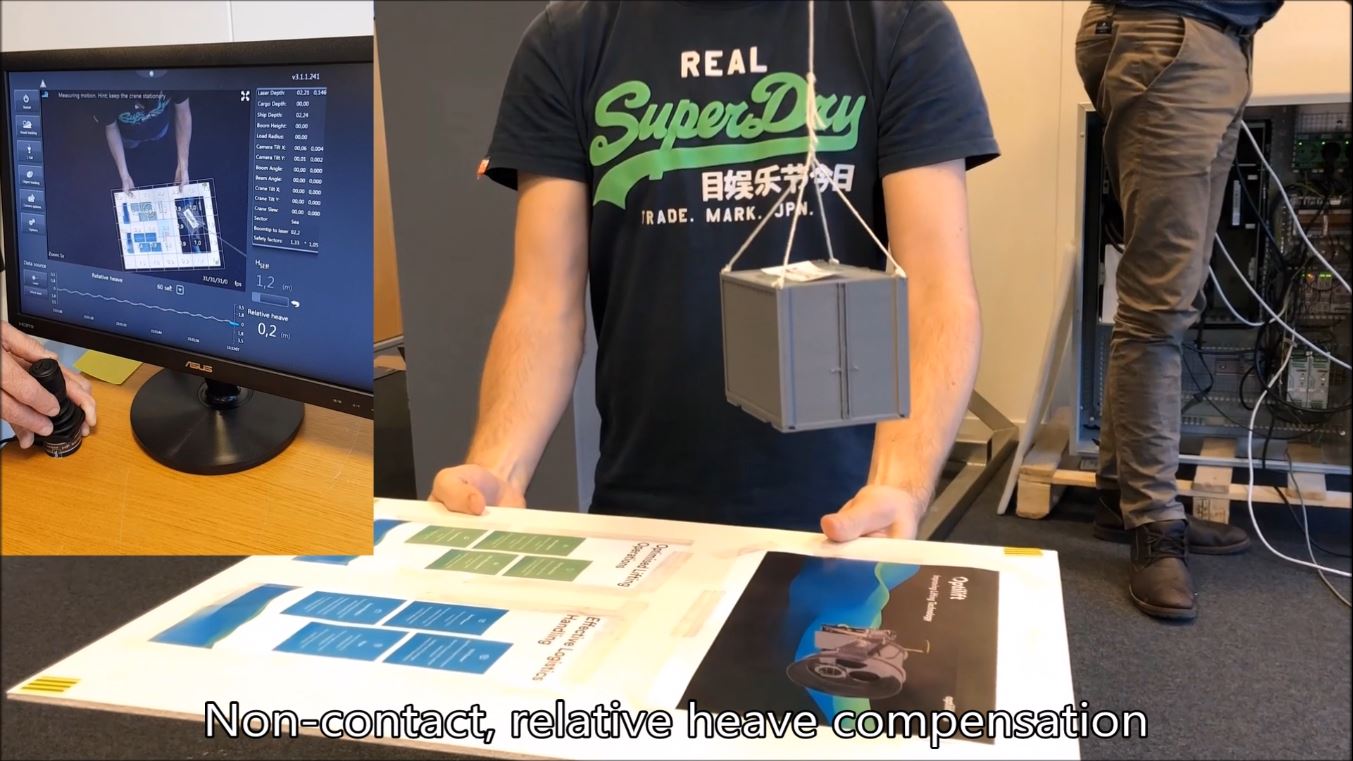
April 5, 2018
The future for offshore and marine lifting- and logistics operations is remotely operated and autonomous.
Timing, lag in network connection or even loss of connectivity makes it crucial to have “smart cranes” to automatically and “locally” compensate for movements and motions real-time. The Optilift sensor technology enables this.
It is also necessary to automate parts of the crane control, such as auto landing and -liftoff, relative heave compensation and anti-oscillation.
Our non-contact vision technology measures the full relative 3D motion of supply vessel deck relative to the crane boom tip, which enables automated control of crane movements in both vertical and horisontal directions.
We made a simple demonstration-video of non-contact, relative heave compensation. In this demo, the poster acts as the supply vessel, and our system automatically compensates for heave movements.
In the video, a joystick is used for landing and lift-off during active heave-compensation. Next step to implement is auto landing and lift-off.
Optilift – Relative heave compensation – Garage demo 1 from Torbjorn Engedal on Vimeo.